Australian Aviation magazine interview with Oceania Aviation's Airborne Systems team: Part 1 of 3
In keeping with newly emerging and developing technologies, the needs and capabilities of helicopter operators are constantly changing. As such, the role equipment industry, which provides modifications and specialist equipment for helicopters, grows more and more important every day. Recently our Airborne Systems team sat down with Hannah Dowling from Australian Aviation, to discuss how we are "making waves" in role equipment design, manufacture and installation across Australasia.
Role equipment, sometimes referred to as modifications or airborne systems, are any “specialist equipment that can expand the role and capability of a helicopter to suit the needs of its operator”, explains Airborne Systems manager Tony van Tiel. “It could be cargo pods, which allow the aircraft to carry hard-to-transport equipment, spray systems for aerial agriculture work, cargo hook systems to allow transport of loads external to the aircraft, or control systems that allow for the operation of these types of equipment.”
“Oceania's Airborne Systems division started off small,” adds design and manufacturing engineer Adam Pattinson. “It was almost like a side project at first. It was essentially an optional additional service for customers who purchased aircraft from us and wanted additional capabilities. So the team would provide modifications, largely cargo swings to start with, for existing customers who needed those additional capabilities.
“Since we were able to produce something that was personalised to their needs, and do it in-house, we were able to keep the costs down for that operator, and over time we just saw more and more customers making requests for this type of equipment.”
“From there, we grew pretty organically,” van Tiel adds. “The hangar got busier, it got bigger, we saw more and more aircraft sold to either tourist operators or agriculture operators, who asked us if we could help them acquire or build what they need, and we were able to design, build and install it all for them.”
Since then, the Airborne Systems division has continued to grow with no signs of slowing, and now boasts a bigger purpose-built workshop – where the team can provide specific and unique solutions for new and existing customers, right through from the design stage, to manufacturing, certification, and installation.
“These days, a lot of our role equipment products are built to order,” says van Tiel. “While we do try to keep stock in-shop, due to demand and our current capacity, it tends to go out the door faster than we can build it. We now have about 400 modifications that we own, as well as a dozen Supplemental Type Certificates (STCs), so it really feels like we’re forever expanding, and even though we recently upgraded our facilities, we already feel like we’re running out of room.”
Understandably, modifying the capability of a helicopter, and thus the weight or balance of the aircraft, requires a vigorous certification process. According to van Tiel, this process can look quite different depending on the nature of the required modification. “The process of certification is dependent on whether the equipment or modification is a ‘one-off’, specific to one customer’s needs, or if it’s a change that can easily be applied to other aircraft of the same type, and that other customers could potentially need and use,” he says.
For modifications developed for one aircraft to be used across any aircraft of the same type, an STC is required, which can take some time to seek and approve, according to van Tiel: “STCs require approval from the regulator, which means the approval process is a bit more stringent than a one-off. It’s because an STC means that the given modification can be fitted to any helicopter within that model range.
Pattinson adds that the STC process generally takes longer as it requires additional testing measures, including flight tests, for bigger equipment. “A spray system for agricultural work, for example, can impact weight and balance a lot more, so flight tests are required before approval. So, while a one-off modification for one customer can take anywhere between one and four weeks, depending on the size of the design change, the process to secure an STC really depends on the time schedule of the regulator, be that NZCAA or CASA,” he explains.
“However, the more information you can provide the regulator, the quicker the process becomes,” van Tiel says. “If they have to keep coming back to you with questions or concerns, it can really drag out the whole process, so it’s better to get it right straight off the bat, and that’s why we try and do as much in-house as we can.”
Meanwhile, one-off modifications require more work for the Airborne Systems team, but approval for operations is generally achieved fairly efficiently through Oceania’s collaboration with Melbourne-based Part 146 company Five Rings Aerospace.
“If it’s a one-off modification, then we will generally come up with a tailored concept for the customer, design it and then get it approved fairly efficiently,” van Tiel explains. “For example, if we were to get an order for a spray system we don’t already produce, that whole process from beginning to end could take about a month to build and install – and cargo pods are even less complicated.
“So, Adam would work with our design partner Five Rings Aerospace to tailor the design of the system to the exact needs of the client, and come up with an initial prototype. All the drawings and documents are finalised, noting all changes and customisations required for certification. On our side of the hangar, we’ll be building the system, and once certification is issued, we can install it. We’ll send those final specs through to the customer, then the aircraft comes in and our team will install it for the customer.”
It's a complex process to go from an idea, through to a design, prototype, approval, manufacture and finally installation - but one that the Airborne Systems team have perfected over the years. It's why Oceania Aviation's customers trust the Part 148-certified team so well, and why word-of-mouth has been such a strong precursor to growth both in New Zealand and across the Tasman!
To find out more about the role equipment our team offer or to get in touch to request a tailored equipment solution, visit our Airborne Systems page.
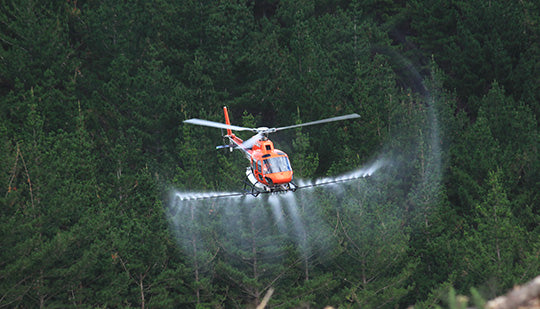
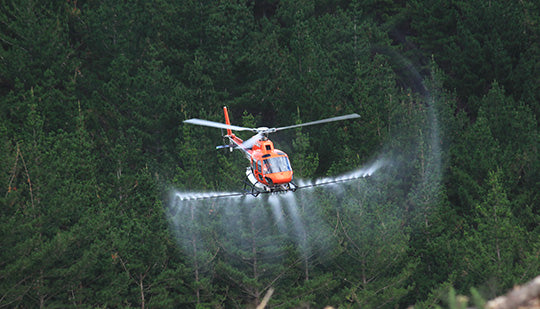
Australian Aviation magazine interview with Oceania Aviation's Airborne Systems team: Part 1 of 3
In keeping with newly emerging and developing technologies, the needs and capabilities of helicopter operators are constantly changing. As such, the role equipment industry, which provides modifications and specialist equipment for helicopters, grows more and more important every day. Recently our Airborne Systems team sat down with Hannah Dowling from Australian Aviation, to discuss how we are "making waves" in role equipment design, manufacture and installation across Australasia.
Role equipment, sometimes referred to as modifications or airborne systems, are any “specialist equipment that can expand the role and capability of a helicopter to suit the needs of its operator”, explains Airborne Systems manager Tony van Tiel. “It could be cargo pods, which allow the aircraft to carry hard-to-transport equipment, spray systems for aerial agriculture work, cargo hook systems to allow transport of loads external to the aircraft, or control systems that allow for the operation of these types of equipment.”
“Oceania's Airborne Systems division started off small,” adds design and manufacturing engineer Adam Pattinson. “It was almost like a side project at first. It was essentially an optional additional service for customers who purchased aircraft from us and wanted additional capabilities. So the team would provide modifications, largely cargo swings to start with, for existing customers who needed those additional capabilities.
“Since we were able to produce something that was personalised to their needs, and do it in-house, we were able to keep the costs down for that operator, and over time we just saw more and more customers making requests for this type of equipment.”
“From there, we grew pretty organically,” van Tiel adds. “The hangar got busier, it got bigger, we saw more and more aircraft sold to either tourist operators or agriculture operators, who asked us if we could help them acquire or build what they need, and we were able to design, build and install it all for them.”
Since then, the Airborne Systems division has continued to grow with no signs of slowing, and now boasts a bigger purpose-built workshop – where the team can provide specific and unique solutions for new and existing customers, right through from the design stage, to manufacturing, certification, and installation.
“These days, a lot of our role equipment products are built to order,” says van Tiel. “While we do try to keep stock in-shop, due to demand and our current capacity, it tends to go out the door faster than we can build it. We now have about 400 modifications that we own, as well as a dozen Supplemental Type Certificates (STCs), so it really feels like we’re forever expanding, and even though we recently upgraded our facilities, we already feel like we’re running out of room.”
Understandably, modifying the capability of a helicopter, and thus the weight or balance of the aircraft, requires a vigorous certification process. According to van Tiel, this process can look quite different depending on the nature of the required modification. “The process of certification is dependent on whether the equipment or modification is a ‘one-off’, specific to one customer’s needs, or if it’s a change that can easily be applied to other aircraft of the same type, and that other customers could potentially need and use,” he says.
For modifications developed for one aircraft to be used across any aircraft of the same type, an STC is required, which can take some time to seek and approve, according to van Tiel: “STCs require approval from the regulator, which means the approval process is a bit more stringent than a one-off. It’s because an STC means that the given modification can be fitted to any helicopter within that model range.
Pattinson adds that the STC process generally takes longer as it requires additional testing measures, including flight tests, for bigger equipment. “A spray system for agricultural work, for example, can impact weight and balance a lot more, so flight tests are required before approval. So, while a one-off modification for one customer can take anywhere between one and four weeks, depending on the size of the design change, the process to secure an STC really depends on the time schedule of the regulator, be that NZCAA or CASA,” he explains.
“However, the more information you can provide the regulator, the quicker the process becomes,” van Tiel says. “If they have to keep coming back to you with questions or concerns, it can really drag out the whole process, so it’s better to get it right straight off the bat, and that’s why we try and do as much in-house as we can.”
Meanwhile, one-off modifications require more work for the Airborne Systems team, but approval for operations is generally achieved fairly efficiently through Oceania’s collaboration with Melbourne-based Part 146 company Five Rings Aerospace.
“If it’s a one-off modification, then we will generally come up with a tailored concept for the customer, design it and then get it approved fairly efficiently,” van Tiel explains. “For example, if we were to get an order for a spray system we don’t already produce, that whole process from beginning to end could take about a month to build and install – and cargo pods are even less complicated.
“So, Adam would work with our design partner Five Rings Aerospace to tailor the design of the system to the exact needs of the client, and come up with an initial prototype. All the drawings and documents are finalised, noting all changes and customisations required for certification. On our side of the hangar, we’ll be building the system, and once certification is issued, we can install it. We’ll send those final specs through to the customer, then the aircraft comes in and our team will install it for the customer.”
It's a complex process to go from an idea, through to a design, prototype, approval, manufacture and finally installation - but one that the Airborne Systems team have perfected over the years. It's why Oceania Aviation's customers trust the Part 148-certified team so well, and why word-of-mouth has been such a strong precursor to growth both in New Zealand and across the Tasman!
To find out more about the role equipment our team offer or to get in touch to request a tailored equipment solution, visit our Airborne Systems page.
- Choosing a selection results in a full page refresh.
- Press the space key then arrow keys to make a selection.